Разработка системы автоматизации технологических операций прокатного стана
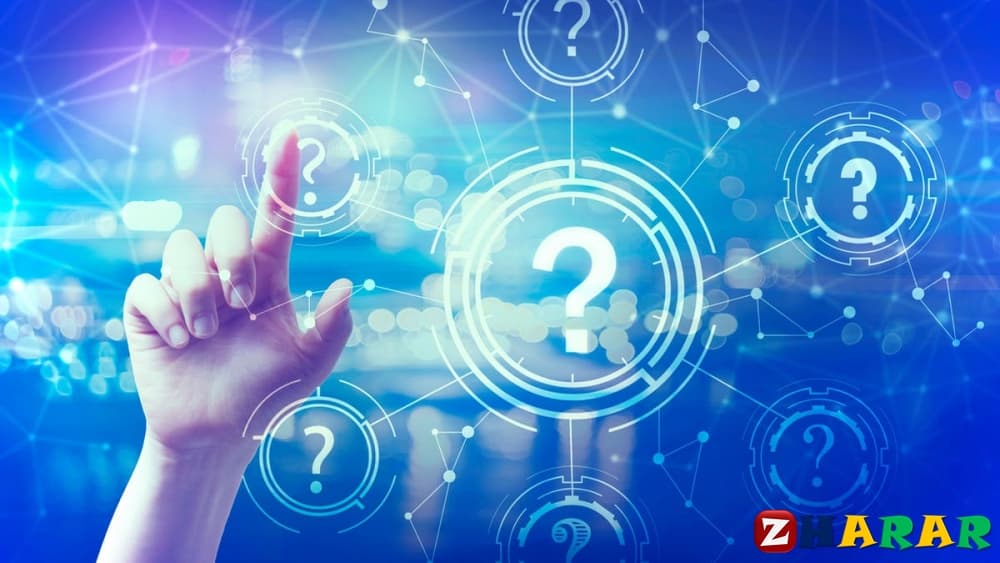
Содержание
Введение
1. Анализ технологического процесса холодной прокатки стальной
полосы, основные проблемы производства и тенденции к их решению
1.1 Технология прокатного производства и актуальность внедрения
автоматической прокатной линии
1.2 Анализ технологического процесса производства холоднокатаной
стальной полосы. Характеристики и требования к изделию.
1.2.1 Прокатка стали и основные тенденции повышения эффективности
холодной прокатки.
1.2.2 Анализ основных путей развития технологии и оборудования цехов
холодной прокатки
1.2.3 Основные характеристики и требования к готовому изделию.
1.3 Выбор структурной схемы технологического процесса производства
холоднокатаной стальной полосы
1.4 Исследование принципов работы и Анализ устройства основного
технологического оборудования принятой прокатной схемы
1.4.1 Травильные агрегаты металлургической промышленности.
1.4.2 Устройства непрерывной подачи стальной полосы.
1.4.3 Непрерывные станы холодной прокатки и дрессировки стальной
полосы.
1.5 Обзор основных дефектов и возможность повышения качества
готовой продукции посредством модернизации устаревшего
оборудования прокатного стана.
1.5.1 Основные дефекты холоднокатаной стальной полосы.
1.5.2 Улучшение планшетности и поперечной разнотолщинности
холоднокатаных полос.
1.6 Разработка математической модели стана холодной прокатки
2 Расчет автоматической линии и регуляторов холодной прокатки
стальной полосы
2.1 Расчет основного и вспомогательного оборудования
2.1.1 Ориентировочный расчет деформационного и скоростного
режимов прокатки
2.1.2 Расчет работы прокатного стана во времени
2.1.3 Расчет электрических и нагревательных элементов линии
2.1.4 Тепловой расчет печи рекристализационного отжига
2.1.5 Расчет количества оборудования
2.1.6 Определение количества и типов приборов контроля
2.2 Расчет системы управления электроприводами прокатного стана
2.2.1 Система двухзонного регулирования скорости с зависимым
ослаблением потока в функции ЭДС якоря двигателя
2.2.2 Расчет регулятора скорости в системе двухзонного регулирования.
2.2.3 Расчет контура регулирования возбуждения
2.2.4. Расчет контура регулирования ЭДС
3 Разработка автоматической линии холодной прокатки и системы
регулирования технологических параметров, выбор основного и
вспомогательного оборудования
3.1 Автоматизация непрерывного широкополосного стана холодной
прокатки
3.1.1. Особенности технологии и оборудования НШСХП
3.1.2. Автоматическое регулирование толщины полосы
3.1.3. Система регулирования натяжения полосы в чистовой группе
клетей
3.1.4. Система автоматического регулирования обжатия
на дрессировочном стане
3.1.5. Система автоматического точного останова стана в конце пропуска
3.2 Автоматическая система управления линией холодной прокатки
4 Технико-экономические показатели и расчет экономической
эффективности
4.1 Расчет капитальных вложений по группам основных фондов.
5 Безопасность и экологичность проекта
5.3 Безопасность в чрезвычайных ситуациях
Заключение.
1. Анализ технологического процесса холодной прокатки
стальной полосы, основные проблемы производства и тенденции к их
решению
1.1 Технология прокатного производства и актуальность
внедрения автоматической прокатной линии
Технология прокатного производства–это комплекс взаимосвязанных технологических переделов, определяющих качество
прокатной продукции и технико-экономические показатели работы
прокатных цехов, металлургических и машиностроительных заводов.
Прокатное производство – это получение путём прокатки из стали и
других металлов различных изделий и полуфабрикатов, а также
дополнительная обработка их с целью повышения качества. Более 70%
выплавляемой стали, в нашей стране, подвергается прокатке. Прокатное
производство обычно организуется на металлургических и
машиностроительных заводах.
В условиях постоянно возрастающих требований к качеству
металлопродукции, оснащение предприятий современным прокатным
оборудованием, создание новых и усовершенствование существующих
технологических процессов, учет всех технологических факторов при
автоматизации производства проката позволит наиболее эффективно решать
вопросы, связанные с работой прокатных цехов, с дальнейшим внедрением
новой техники и достижений науки в производстве, тем самым обеспечивая
более высокий уровень качества проката, эффективность его производства и
использования.
Сортамент выпускаемой продукции на непрерывных сортовых
прокатных станах диктуется потребностями машиностроительного
производства и включает в себя широкий спектр фасонных профилей,
листов, полос и катанки. Прокаткой получают разнообразные виды
заготовок, которые являются исходным материалом для других способов
обработки. Так, горячекатаная и холоднокатаная листовая сталь, полосы и
ленты в больших количествах идут для листовой штамповки. Рентабельность
продукции, выпускаемой машиностроительным производством во многом
зависит от качества получаемого проката, производительности стана и
энергозатрат.
Изучение вопросов технологии производства проката с оценкой
влияния основных технологических процессов и операций по всем переделам
прокатного производства на качество готовой прокатной продукции, на
возможности расширения марочного и размерного сортамента проката и
эффективность производства – важное условие, предшествующее внедрению
автоматических металлопрокатных линий.
Данные обстоятельства привели к появлению более жестких
требований к системам управления режимами работы электроприводов
прокатных клетей и необходимости комплексного изучения, анализа и
совершенствования существующих способов управления технологическими
переменными процесса прокатки.
На большинстве отечественных непрерывных сортовых прокатных
станах системы автоматизированного регулирования натяжения полосы в
межклетевом промежутке выполнены по принципу косвенной оценки
величины натяжения по изменяющимся энергосиловым параметрам привода
предыдущей клети. Данные системы включают в себя контур регулирования
натяжения, который, корректируя скорость последующей клети,
поддерживает натяжение в заданном диапазоне. Данный принцип управления
при высоких скоростях прокатки не позволяет исключить наличия в
переходных режимах продольных динамических ударов в металле, которые
могут привести к вытяжке полосы или ее разрыву в том случае, если
натяжение превысит допустимое значение. Это обстоятельство ограничивает
сферу применения данных систем и требует их совершенствования.
Для повышения эффективности от внедрения автоматических
прокатных линий средней производительности необходимо чтобы сортамент
производимой ими продукции был максимально широким в пределах
технологических возможностей. При использовании непрерывных
прокатных станов это требует частой перенастройки стана и усложняет
подготовку производства. Применение современных технических средств
позволяет автоматизировать процесс разработки калибровки и настройки
прокатного стана.
Применение современных компьютеризированных систем
управления, обладающих более высоким качеством управления, нежели
аналоговые, совместно с высокоточными импульсными датчиками, позволит
приблизить режим прокатки к режиму свободной прокатки и сделать его
более устойчивым. Режим свободной прокатки способствует лучшему
заполнения калибров и исключению продольных динамических ударов на
участке металлической полосы, который находится между соседними
клетями. В связи с этим, актуальной задачей является изучение возможности
прокатки без петлеобразования тонких сортовых профилей в чистовых
группах клетей непрерывных станов.
Кроме того, при разработке систем управления режимами прокатки
на непрерывных прокатных станах также остро стоит вопрос минимизации
удельных энергозатрат с целью снижения себестоимости готового сортового
проката. Это и многое другое говорит о необходимости дальнейшего
исследования и совершенствования систем управления режимами работы
электроприводов прокатных станков и непрерывных сортовых прокатных
стано
1.2 Анализ технологического процесса производства
холоднокатаной стальной полосы. Характеристики и требования к
изделию
1.2.1 Прокатка стали и основные тенденции повышения
эффективности холодной прокатки.
Высокая производительность процессов обработки металлов
давлением, сравнительно низкая их энергоемкость, а также незначительные
потери металла при производстве изделий выгодно отличают их по
сравнению, например, с обработкой металла резанием, когда требуемую
форму изделия получают удалением значительной части заготовки в
стружку. Существенным достоинством пластической обработки является
значительное улучшение свойств металла в процессе деформирования.
На металлургическом заводе получение готового холодного проката
выполняется по двум технологическим схемам «слиток – горячий прокат –
готовый холодный прокат» и «литая заготовка – горячий прокат – готовый
холодный прокат».
При первой схеме проката выбирается слиток определенной массы
и с таким расчетом, чтобы непосредственно из него можно было получить
необходимое изделие за один нагрев, за которым далее следует холодная
прокатка стали. Однако при слитках массой 6–10 тонн и более получение
готового проката за один нагрев не всегда представляется возможным. По
этой причине дополнительно используются обжимные станы, задача которых
состоит в обработке слитка в заготовку. К тому же при последующей
холодной прокатке требуется дополнительная травка и очистка листа от
наклепа и обрезка кромок. Данное обстоятельство расширяет
технологической схему: слиток
–горячекатаный полупродукт
–дополнительная обработка полупродукта – готовый холодный прокат. Это
повышает энергоемкость и трудоемкость прокатной схемы и следовательно
стоимость готового изделия. Поэтому в последнее время все большее
предпочтение уделяется второй технологической схеме.
Применению второй схемы проката способствует успешное
освоение разливки стали в заготовки квадратного и прямоугольного сечений,
что до некоторых пор имело распространение лишь в цветной металлургии.
Непрерывное литье стальных заготовок длительное время не применялось
из-за значительных трудностей выполнения технологического процесса
самой разливки. Однако этот процесс обеспечивает получение химически
более однородной плотной заготовки, что резко повышает выход годного
проката. Например, на слябах спокойной углеродистой стали выход годного
проката выше на 20%, чем при разливке в изложницы. Вместе с тем
исключается необходимость иметь отделение подготовки изложниц и
поддонов, стрипперное отделение, отпадает необходимость в
дополнительной травке и очистке листа от наклепа и обрезке кромок.
Применение непрерывной разливки стали снижает себестоимость
металлургического передела, так как при этом устраняется необходимость в
дорогостоящем оборудовании обжимных цехов и резательных цехов,
исключаются расходы на содержание обслуживающего и административного
персонала. Установлено, что себестоимость проката в этих условиях
снижается на 18–20% при улучшении во многих случаях механических
свойств и других характеристик стали.
Непрерывным литьем стали изготовляют слябы сечением до
300х2030, 300х2320 мм и квадратные заготовки сечением до 320х320 мм.
После прохождения горячей прокатки заготовка толщиной 1,0–4,5мм
сматывается в рулон и отправляется на стан холодной прокатки. Причиной
этому служит то, что при сравнительно малой толщине прокатываемого
продукта, когда из-за большого отношения поверхности к объему быстрое
охлаждение металла не дает возможность обеспечить высокую температуру в
деформационной зоне, используется холодная прокатка. Холодная прокатка
придает изделиям высокие точность размеров и качество поверхности, что
невозможно при горячей прокатке, а также особые физические свойства.
Технологическая схема получения готового холоднокатаного
листового проката предусматривает:
а) термическая обработка перед прокаткой;
б) холодная прокатка;
в) калибровка и производство профилей;
г) отделка с операциями резки, правки, термической
обработки, удаления поверхностных дефектов, травления и пр.
В последние годы производство холоднокатаного листа составляет
около 40% и все более увеличивается. Это связано с тем, что во многих
отраслях постоянно растет потребность в тонколистовой стали с высокими
механическими свойствами, точными размерами, хорошим качеством
поверхности.
Среди возможных направлений повышения эффективности
производства холоднокатаной листовой стали можно обозначить следующие
основные тенденции:
а) строительство современных непрерывных станов с 6-7
клетями, скоростью прокатки до 50 м/с и массой рулона до 60 т;
б) использование жестких клетей с полуизгибом валков;
в) использование на станах датчиков авторегулирования
натяжения, толщины и ширины полосы;
г) использование непрерывных поточных линий
термообработки вертикального или горизонтального типа.
1.2.2 Анализ основных путей развития технологии и оборудования цехов холодной прокатки
Холоднокатаный листовой прокат относится к категории
высококачественной металлопродукции. Использование его в различных
отраслях промышленности чрезвычайно эффективно. Это является стимулом
интенсивного научно-технического прогресса в области производства
холоднокатаных листов. Анализ современных тенденций в
совершенствовании данного вида производства позволяет выделить
следующие основные направления:
Замене трудоемкой и экологически вредной операции травления другими способами удаления
окалины с поверхности горячекатаных полос-заготовок. Установка в составе
травильных линий валковых окалиноломателей, работающих по принципу
резкого перегиба и растяжения полосы, и дрессировочных клетей позволяет
значительно сократить процедуру последующего травления. В последние
годы развивается дробеструйный способ удаления окалины. Дробеструйные
аппараты устанавливаются либо непосредственно в линиях травления, либо
отдельно, в самостоятельных линиях. Обычно после дробеструйной
обработки требуется лишь легкое травление; при этом расход кислоты
сокращается примерно на 75 %.
В цехах с целесообразно сооружать новые непрерывные станы, в основном 5-клетевые для прокатки
полос толщиной не менее 0,3- 0,4 мм для прокатки более тонких полос,
оборудованные мощными намоточно-натяжными барабанами (моталками).
Масса рулонов достигнет 50-60 т. Максимальная скорость прокатки, с
внедрением нового оборудования не превысит 35-40 м/с, так как практика
свидетельствует, что достижение таких скоростей вызывает трудности.
В связи с постоянным ужесточением требований по минимальной поперечной разнотолщинности
листов, а также их полной планшетности, необходимо проводить работы по
совершенствованию профилировок валков. Особого внимания заслуживает
разработка способов мобильного воздействия на профиль прокатной щели и,
соответственно, профиль листов в процессе прокатки. Необходимо
расширять применение установок противоизгиба валков.
Тенденция к постепенному уменьшению толщины прокатываемых листов вызывает необходимость
применения более эффективных технологических смазок (эмульсий). Однако
введение дополнительных количеств жировых компонентов в смазку может
привести к повышенной зажиренности металла после прокатки, что
нежелательно. Для устранения указанного противоречия современные
смазочные системы на непрерывных станах должны предусматривать
возможность раздельной подачи смазки по клетям, позволяя варьировать
состав и концентрацию смазки. В этом случае на валки последней, чистовой
клети будет подаваться низкоконцентрированная эмульсия или даже
моющий раствор. Кроме того современные смазочные системы также
должны обеспечивать достаточное охлаждение и тщательную очистку
эмульсии от металлических частиц и других загрязнений.
В термических отделениях необходимо применять агрегаты непрерывного отжига с вертикальными или
горизонтальными протяжными печами. Практика подтвердила большие
преимущества этих агрегатов: возможность достаточно простого
регулирования температурно-скоростных параметров обработки, удобство
механизации и автоматизации, высокую производительность.
Основные объекты
современных цехов холодной прокатки, будучи агрегатами непрерывного
действия и имея соизмеримую производительность, могут быть объединены
в единые, совмещенные линии. Например, включение дрессировочных
станов в состав агрегатов непрерывного отжига, или совмещение станов
холодной прокатки с агрегатами непрерывного травления. Имеются
сведения, что при создании совмещенных линий травления-прокатки
капитальные затраты снижаются на 18 %.
Нормальное функционирование новых, высокопроизводительных цехов холодной
прокатки невозможно без использования автоматических систем управления
технологическим процессом (АСУ ТП). Применение АСУ дает
положительные результаты на всех переделах, но особенно необходимо оно
на основном технологическом агрегате –непрерывном или реверсивном
прокатном стане, где в настоящее время операции во многом производятся
вручную. Качество выпускаемой продукции в решающей степени зависит от
работы автоматических систем, управляющих самим процессом прокатки. К
их числу относятся:
а)полосы (САРТ);система автоматического регулирования толщины(САРН);
б)система автоматического регулирования натяжения
в)система автоматического регулирования профиля и формы полосы (САРПФ);
г)система автоматической подачи смазочно-
охлаждающей жидкости (САПОЖ).
В задачу САРТ входит обеспечение постоянства толщины
прокатываемых полос, исключение значительных колебаний по толщине.
Работа этой системы осуществляется посредством воздействия на нажимные
устройства, а также путем изменения межклетевых натяжений и скорости
вращения валков. По некоторым данным, применение САРТ обеспечивает
прокатку 99% длины полосы с отклонениями от заданной толщины не более
1-2 %.
САРН является как бы подсистемой САРТ, работа этих систем
тесно взаимосвязана. Поддержание величины натяжений на заданном,
оптимальном уровне особенно необходимо в переходных режимах прокатки,
например при переходе с заправочной скорости на рабочую. САРПФ
воздействует на профиль межвалкового зазора (прокатной щели). Одним из
наиболее эффективных средств регулирования в этом случае является
применение устройств для противоизгиба (или принудительного изгиба)
валков.
САПОЖ обеспечивает подачу смазочно-охлаждающей жидкости
(СОЖ) на валки и полосу в необходимом, регулируемом количестве. Подача
СОЖ ведется раздельно по зонам, выделенным по длине бочки валков. В
задачу САПОЖ входит стабилизация теплового состояния валков в процессе
прокатки. Для выполнения этой функции вдоль бочки валков располагаются
температурные датчики. Регулирование температуры валков осуществляется
с точностью ± 5 °С. «Мозгом» автоматических систем управления являются
ЭВМ, которые на современных быстроходных станах составляют мощные
вычислительные комплексы. Затраты на автоматизацию станов холодной
прокатки окупаются за 2-3 года, не считая тех выгод, которые получает
потребитель благодаря применению листовой продукции более высокого
качества.....
Введение
1. Анализ технологического процесса холодной прокатки стальной
полосы, основные проблемы производства и тенденции к их решению
1.1 Технология прокатного производства и актуальность внедрения
автоматической прокатной линии
1.2 Анализ технологического процесса производства холоднокатаной
стальной полосы. Характеристики и требования к изделию.
1.2.1 Прокатка стали и основные тенденции повышения эффективности
холодной прокатки.
1.2.2 Анализ основных путей развития технологии и оборудования цехов
холодной прокатки
1.2.3 Основные характеристики и требования к готовому изделию.
1.3 Выбор структурной схемы технологического процесса производства
холоднокатаной стальной полосы
1.4 Исследование принципов работы и Анализ устройства основного
технологического оборудования принятой прокатной схемы
1.4.1 Травильные агрегаты металлургической промышленности.
1.4.2 Устройства непрерывной подачи стальной полосы.
1.4.3 Непрерывные станы холодной прокатки и дрессировки стальной
полосы.
1.5 Обзор основных дефектов и возможность повышения качества
готовой продукции посредством модернизации устаревшего
оборудования прокатного стана.
1.5.1 Основные дефекты холоднокатаной стальной полосы.
1.5.2 Улучшение планшетности и поперечной разнотолщинности
холоднокатаных полос.
1.6 Разработка математической модели стана холодной прокатки
2 Расчет автоматической линии и регуляторов холодной прокатки
стальной полосы
2.1 Расчет основного и вспомогательного оборудования
2.1.1 Ориентировочный расчет деформационного и скоростного
режимов прокатки
2.1.2 Расчет работы прокатного стана во времени
2.1.3 Расчет электрических и нагревательных элементов линии
2.1.4 Тепловой расчет печи рекристализационного отжига
2.1.5 Расчет количества оборудования
2.1.6 Определение количества и типов приборов контроля
2.2 Расчет системы управления электроприводами прокатного стана
2.2.1 Система двухзонного регулирования скорости с зависимым
ослаблением потока в функции ЭДС якоря двигателя
2.2.2 Расчет регулятора скорости в системе двухзонного регулирования.
2.2.3 Расчет контура регулирования возбуждения
2.2.4. Расчет контура регулирования ЭДС
3 Разработка автоматической линии холодной прокатки и системы
регулирования технологических параметров, выбор основного и
вспомогательного оборудования
3.1 Автоматизация непрерывного широкополосного стана холодной
прокатки
3.1.1. Особенности технологии и оборудования НШСХП
3.1.2. Автоматическое регулирование толщины полосы
3.1.3. Система регулирования натяжения полосы в чистовой группе
клетей
3.1.4. Система автоматического регулирования обжатия
на дрессировочном стане
3.1.5. Система автоматического точного останова стана в конце пропуска
3.2 Автоматическая система управления линией холодной прокатки
4 Технико-экономические показатели и расчет экономической
эффективности
4.1 Расчет капитальных вложений по группам основных фондов.
5 Безопасность и экологичность проекта
5.3 Безопасность в чрезвычайных ситуациях
Заключение.
1. Анализ технологического процесса холодной прокатки
стальной полосы, основные проблемы производства и тенденции к их
решению
1.1 Технология прокатного производства и актуальность
внедрения автоматической прокатной линии
Технология прокатного производства–это комплекс взаимосвязанных технологических переделов, определяющих качество
прокатной продукции и технико-экономические показатели работы
прокатных цехов, металлургических и машиностроительных заводов.
Прокатное производство – это получение путём прокатки из стали и
других металлов различных изделий и полуфабрикатов, а также
дополнительная обработка их с целью повышения качества. Более 70%
выплавляемой стали, в нашей стране, подвергается прокатке. Прокатное
производство обычно организуется на металлургических и
машиностроительных заводах.
В условиях постоянно возрастающих требований к качеству
металлопродукции, оснащение предприятий современным прокатным
оборудованием, создание новых и усовершенствование существующих
технологических процессов, учет всех технологических факторов при
автоматизации производства проката позволит наиболее эффективно решать
вопросы, связанные с работой прокатных цехов, с дальнейшим внедрением
новой техники и достижений науки в производстве, тем самым обеспечивая
более высокий уровень качества проката, эффективность его производства и
использования.
Сортамент выпускаемой продукции на непрерывных сортовых
прокатных станах диктуется потребностями машиностроительного
производства и включает в себя широкий спектр фасонных профилей,
листов, полос и катанки. Прокаткой получают разнообразные виды
заготовок, которые являются исходным материалом для других способов
обработки. Так, горячекатаная и холоднокатаная листовая сталь, полосы и
ленты в больших количествах идут для листовой штамповки. Рентабельность
продукции, выпускаемой машиностроительным производством во многом
зависит от качества получаемого проката, производительности стана и
энергозатрат.
Изучение вопросов технологии производства проката с оценкой
влияния основных технологических процессов и операций по всем переделам
прокатного производства на качество готовой прокатной продукции, на
возможности расширения марочного и размерного сортамента проката и
эффективность производства – важное условие, предшествующее внедрению
автоматических металлопрокатных линий.
Данные обстоятельства привели к появлению более жестких
требований к системам управления режимами работы электроприводов
прокатных клетей и необходимости комплексного изучения, анализа и
совершенствования существующих способов управления технологическими
переменными процесса прокатки.
На большинстве отечественных непрерывных сортовых прокатных
станах системы автоматизированного регулирования натяжения полосы в
межклетевом промежутке выполнены по принципу косвенной оценки
величины натяжения по изменяющимся энергосиловым параметрам привода
предыдущей клети. Данные системы включают в себя контур регулирования
натяжения, который, корректируя скорость последующей клети,
поддерживает натяжение в заданном диапазоне. Данный принцип управления
при высоких скоростях прокатки не позволяет исключить наличия в
переходных режимах продольных динамических ударов в металле, которые
могут привести к вытяжке полосы или ее разрыву в том случае, если
натяжение превысит допустимое значение. Это обстоятельство ограничивает
сферу применения данных систем и требует их совершенствования.
Для повышения эффективности от внедрения автоматических
прокатных линий средней производительности необходимо чтобы сортамент
производимой ими продукции был максимально широким в пределах
технологических возможностей. При использовании непрерывных
прокатных станов это требует частой перенастройки стана и усложняет
подготовку производства. Применение современных технических средств
позволяет автоматизировать процесс разработки калибровки и настройки
прокатного стана.
Применение современных компьютеризированных систем
управления, обладающих более высоким качеством управления, нежели
аналоговые, совместно с высокоточными импульсными датчиками, позволит
приблизить режим прокатки к режиму свободной прокатки и сделать его
более устойчивым. Режим свободной прокатки способствует лучшему
заполнения калибров и исключению продольных динамических ударов на
участке металлической полосы, который находится между соседними
клетями. В связи с этим, актуальной задачей является изучение возможности
прокатки без петлеобразования тонких сортовых профилей в чистовых
группах клетей непрерывных станов.
Кроме того, при разработке систем управления режимами прокатки
на непрерывных прокатных станах также остро стоит вопрос минимизации
удельных энергозатрат с целью снижения себестоимости готового сортового
проката. Это и многое другое говорит о необходимости дальнейшего
исследования и совершенствования систем управления режимами работы
электроприводов прокатных станков и непрерывных сортовых прокатных
стано
1.2 Анализ технологического процесса производства
холоднокатаной стальной полосы. Характеристики и требования к
изделию
1.2.1 Прокатка стали и основные тенденции повышения
эффективности холодной прокатки.
Высокая производительность процессов обработки металлов
давлением, сравнительно низкая их энергоемкость, а также незначительные
потери металла при производстве изделий выгодно отличают их по
сравнению, например, с обработкой металла резанием, когда требуемую
форму изделия получают удалением значительной части заготовки в
стружку. Существенным достоинством пластической обработки является
значительное улучшение свойств металла в процессе деформирования.
На металлургическом заводе получение готового холодного проката
выполняется по двум технологическим схемам «слиток – горячий прокат –
готовый холодный прокат» и «литая заготовка – горячий прокат – готовый
холодный прокат».
При первой схеме проката выбирается слиток определенной массы
и с таким расчетом, чтобы непосредственно из него можно было получить
необходимое изделие за один нагрев, за которым далее следует холодная
прокатка стали. Однако при слитках массой 6–10 тонн и более получение
готового проката за один нагрев не всегда представляется возможным. По
этой причине дополнительно используются обжимные станы, задача которых
состоит в обработке слитка в заготовку. К тому же при последующей
холодной прокатке требуется дополнительная травка и очистка листа от
наклепа и обрезка кромок. Данное обстоятельство расширяет
технологической схему: слиток
–горячекатаный полупродукт
–дополнительная обработка полупродукта – готовый холодный прокат. Это
повышает энергоемкость и трудоемкость прокатной схемы и следовательно
стоимость готового изделия. Поэтому в последнее время все большее
предпочтение уделяется второй технологической схеме.
Применению второй схемы проката способствует успешное
освоение разливки стали в заготовки квадратного и прямоугольного сечений,
что до некоторых пор имело распространение лишь в цветной металлургии.
Непрерывное литье стальных заготовок длительное время не применялось
из-за значительных трудностей выполнения технологического процесса
самой разливки. Однако этот процесс обеспечивает получение химически
более однородной плотной заготовки, что резко повышает выход годного
проката. Например, на слябах спокойной углеродистой стали выход годного
проката выше на 20%, чем при разливке в изложницы. Вместе с тем
исключается необходимость иметь отделение подготовки изложниц и
поддонов, стрипперное отделение, отпадает необходимость в
дополнительной травке и очистке листа от наклепа и обрезке кромок.
Применение непрерывной разливки стали снижает себестоимость
металлургического передела, так как при этом устраняется необходимость в
дорогостоящем оборудовании обжимных цехов и резательных цехов,
исключаются расходы на содержание обслуживающего и административного
персонала. Установлено, что себестоимость проката в этих условиях
снижается на 18–20% при улучшении во многих случаях механических
свойств и других характеристик стали.
Непрерывным литьем стали изготовляют слябы сечением до
300х2030, 300х2320 мм и квадратные заготовки сечением до 320х320 мм.
После прохождения горячей прокатки заготовка толщиной 1,0–4,5мм
сматывается в рулон и отправляется на стан холодной прокатки. Причиной
этому служит то, что при сравнительно малой толщине прокатываемого
продукта, когда из-за большого отношения поверхности к объему быстрое
охлаждение металла не дает возможность обеспечить высокую температуру в
деформационной зоне, используется холодная прокатка. Холодная прокатка
придает изделиям высокие точность размеров и качество поверхности, что
невозможно при горячей прокатке, а также особые физические свойства.
Технологическая схема получения готового холоднокатаного
листового проката предусматривает:
а) термическая обработка перед прокаткой;
б) холодная прокатка;
в) калибровка и производство профилей;
г) отделка с операциями резки, правки, термической
обработки, удаления поверхностных дефектов, травления и пр.
В последние годы производство холоднокатаного листа составляет
около 40% и все более увеличивается. Это связано с тем, что во многих
отраслях постоянно растет потребность в тонколистовой стали с высокими
механическими свойствами, точными размерами, хорошим качеством
поверхности.
Среди возможных направлений повышения эффективности
производства холоднокатаной листовой стали можно обозначить следующие
основные тенденции:
а) строительство современных непрерывных станов с 6-7
клетями, скоростью прокатки до 50 м/с и массой рулона до 60 т;
б) использование жестких клетей с полуизгибом валков;
в) использование на станах датчиков авторегулирования
натяжения, толщины и ширины полосы;
г) использование непрерывных поточных линий
термообработки вертикального или горизонтального типа.
1.2.2 Анализ основных путей развития технологии и оборудования цехов холодной прокатки
Холоднокатаный листовой прокат относится к категории
высококачественной металлопродукции. Использование его в различных
отраслях промышленности чрезвычайно эффективно. Это является стимулом
интенсивного научно-технического прогресса в области производства
холоднокатаных листов. Анализ современных тенденций в
совершенствовании данного вида производства позволяет выделить
следующие основные направления:
Замене трудоемкой и экологически вредной операции травления другими способами удаления
окалины с поверхности горячекатаных полос-заготовок. Установка в составе
травильных линий валковых окалиноломателей, работающих по принципу
резкого перегиба и растяжения полосы, и дрессировочных клетей позволяет
значительно сократить процедуру последующего травления. В последние
годы развивается дробеструйный способ удаления окалины. Дробеструйные
аппараты устанавливаются либо непосредственно в линиях травления, либо
отдельно, в самостоятельных линиях. Обычно после дробеструйной
обработки требуется лишь легкое травление; при этом расход кислоты
сокращается примерно на 75 %.
В цехах с целесообразно сооружать новые непрерывные станы, в основном 5-клетевые для прокатки
полос толщиной не менее 0,3- 0,4 мм для прокатки более тонких полос,
оборудованные мощными намоточно-натяжными барабанами (моталками).
Масса рулонов достигнет 50-60 т. Максимальная скорость прокатки, с
внедрением нового оборудования не превысит 35-40 м/с, так как практика
свидетельствует, что достижение таких скоростей вызывает трудности.
В связи с постоянным ужесточением требований по минимальной поперечной разнотолщинности
листов, а также их полной планшетности, необходимо проводить работы по
совершенствованию профилировок валков. Особого внимания заслуживает
разработка способов мобильного воздействия на профиль прокатной щели и,
соответственно, профиль листов в процессе прокатки. Необходимо
расширять применение установок противоизгиба валков.
Тенденция к постепенному уменьшению толщины прокатываемых листов вызывает необходимость
применения более эффективных технологических смазок (эмульсий). Однако
введение дополнительных количеств жировых компонентов в смазку может
привести к повышенной зажиренности металла после прокатки, что
нежелательно. Для устранения указанного противоречия современные
смазочные системы на непрерывных станах должны предусматривать
возможность раздельной подачи смазки по клетям, позволяя варьировать
состав и концентрацию смазки. В этом случае на валки последней, чистовой
клети будет подаваться низкоконцентрированная эмульсия или даже
моющий раствор. Кроме того современные смазочные системы также
должны обеспечивать достаточное охлаждение и тщательную очистку
эмульсии от металлических частиц и других загрязнений.
В термических отделениях необходимо применять агрегаты непрерывного отжига с вертикальными или
горизонтальными протяжными печами. Практика подтвердила большие
преимущества этих агрегатов: возможность достаточно простого
регулирования температурно-скоростных параметров обработки, удобство
механизации и автоматизации, высокую производительность.
Основные объекты
современных цехов холодной прокатки, будучи агрегатами непрерывного
действия и имея соизмеримую производительность, могут быть объединены
в единые, совмещенные линии. Например, включение дрессировочных
станов в состав агрегатов непрерывного отжига, или совмещение станов
холодной прокатки с агрегатами непрерывного травления. Имеются
сведения, что при создании совмещенных линий травления-прокатки
капитальные затраты снижаются на 18 %.
Нормальное функционирование новых, высокопроизводительных цехов холодной
прокатки невозможно без использования автоматических систем управления
технологическим процессом (АСУ ТП). Применение АСУ дает
положительные результаты на всех переделах, но особенно необходимо оно
на основном технологическом агрегате –непрерывном или реверсивном
прокатном стане, где в настоящее время операции во многом производятся
вручную. Качество выпускаемой продукции в решающей степени зависит от
работы автоматических систем, управляющих самим процессом прокатки. К
их числу относятся:
а)полосы (САРТ);система автоматического регулирования толщины(САРН);
б)система автоматического регулирования натяжения
в)система автоматического регулирования профиля и формы полосы (САРПФ);
г)система автоматической подачи смазочно-
охлаждающей жидкости (САПОЖ).
В задачу САРТ входит обеспечение постоянства толщины
прокатываемых полос, исключение значительных колебаний по толщине.
Работа этой системы осуществляется посредством воздействия на нажимные
устройства, а также путем изменения межклетевых натяжений и скорости
вращения валков. По некоторым данным, применение САРТ обеспечивает
прокатку 99% длины полосы с отклонениями от заданной толщины не более
1-2 %.
САРН является как бы подсистемой САРТ, работа этих систем
тесно взаимосвязана. Поддержание величины натяжений на заданном,
оптимальном уровне особенно необходимо в переходных режимах прокатки,
например при переходе с заправочной скорости на рабочую. САРПФ
воздействует на профиль межвалкового зазора (прокатной щели). Одним из
наиболее эффективных средств регулирования в этом случае является
применение устройств для противоизгиба (или принудительного изгиба)
валков.
САПОЖ обеспечивает подачу смазочно-охлаждающей жидкости
(СОЖ) на валки и полосу в необходимом, регулируемом количестве. Подача
СОЖ ведется раздельно по зонам, выделенным по длине бочки валков. В
задачу САПОЖ входит стабилизация теплового состояния валков в процессе
прокатки. Для выполнения этой функции вдоль бочки валков располагаются
температурные датчики. Регулирование температуры валков осуществляется
с точностью ± 5 °С. «Мозгом» автоматических систем управления являются
ЭВМ, которые на современных быстроходных станах составляют мощные
вычислительные комплексы. Затраты на автоматизацию станов холодной
прокатки окупаются за 2-3 года, не считая тех выгод, которые получает
потребитель благодаря применению листовой продукции более высокого
качества.....
Толық нұсқасын 30 секундтан кейін жүктей аласыз!!!
Қарап көріңіз 👇
Пайдалы сілтемелер:
» Туған күнге 99 тілектер жинағы: өз сөзімен, қысқаша, қарапайым туған күнге тілек
» Абай Құнанбаев барлық өлеңдер жинағын жүктеу, оқу
» Дастархан батасы: дастарханға бата беру, ас қайыру
Ілмектер: скачать Разработка системы автоматизации технологических операций прокатного стана бесплатно дипломную работу, база готовых дипломных работ бесплатно, готовые дипломные работы скачать бесплатно, дипломная работа скачать бесплатно казахстан, Разработка системы автоматизации технологических операций прокатного стана