Разработка системы мониторинга механических величин турбины
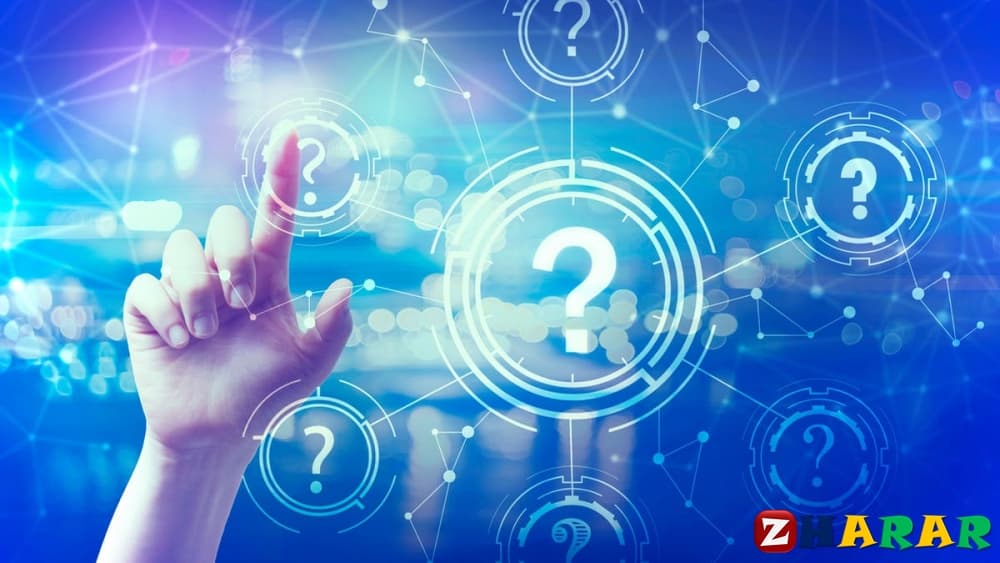
Содержание
Введение
1.1. Описание основного оборудования АТЭЦ-2.
1.2. Технические описания и характеристики турбин.
1.3. Техническое описание и характеристика котлов БКЗ-420-140
1.4. Технологическое описание турбины.
1.4.1 Классификация паровых турбин.
1.4.2. Тепловой процесс паровых турбин.
1.5 . Система защиты турбины
1.6 Механические величины турбины и обоснование замены 20
оборудования
1.6.1 Контролируемые объекты на турбине.
1.6.2 Обоснование замены оборудования
2. Анализ и выбор оборудования.
2.1. Первичное оборудование
2.2. Вторичное оборудование ЛМЗ-97.09С
2.2.1 Общие сведения об аппаратуре "ЛМЗ-97.09С"
2.2.2 Описание и работа
2.2.3 Шкаф аппаратный
2.3 Схемы подключения оборудования ЛМЗ
3. Анализ и разработка программного обеспечения мониторинга
механических величин турбины
4. Безопасность жизнедеятельности
4.1. Анализ условий труда
4.2. Расчет выбросов в атмосферу
4.2.1 Выброс золы в атмосферу
4.2.2 Выброс сернистого ангидрида в атмосферу.
4.2.3 Количество выбросов оксидов азота на ТЭЦ
4.2.4 Количество выбросов оксидов ванадия
4.2.5 Определение минимальной высоты трубы
4.3. Расчёт максимальной концентрации вредных веществ
5. Технико-экономическое обоснование
5.1. Цели и задачи проекта
5.2. Производимые продукты
5.3 Расчет затрат на производство тепла и электричества
5.3.1. Техническое описание производства
5.3.2. Определение затрат на топливо
5.3.3 Расчет КПД использования топлива.
5.3.4 Расчет затрат на воду.
5.3.5 Расчет затрат на заработную плату.
5.3.6 Расчет амортизационных отчислений.
5.3.7 Расчет затрат на проведение текущего ремонта.
5.3.8 Расчет платы за выбросы.
5.3.9 Общестанционные и цеховые расходы.
5.4. Расчет себестоимости отпуска энергии.
5.5. Расчет затрат на систему мониторинга.
5.5.1 Расчет затрат на оборудование ЛМЗ97 -09С
5.6. Ожидаемый экономический эффект модернизации турбины
Заключение.
Список литературы
Приложение А
Приложение Б
Приложение В
Приложение Г
Приложение Д
Приложение Е
Приложение Ж
Приложение З
Приложение И
Приложение К
1. Общая часть. Описание объекта автоматизации
1.1 Описание основного оборудования АТЭЦ-2
а) шесть паровых турбин три турбины типа ПТ-80/100-130/13; одна
турбина типа Р-50-130; две турбины типа Т-100/120-130.
б) семь паровых котлов типа БКЗ-420-140.
1.2 Технические описания и характеристики турбин
Паровая турбина ПТ-80/100-130/13, конденсационная с регулируемыми
отборами пара производственным и отопительными, номинальной
мощностью 80 МВт. Представляет собой одновальный двухцилиндровый
агрегат и предназначен для непосредственного привода генератора типа
ТВФ-120-2 мощностью 120 МВт.
Турбина ПТ-80/100-130/130 имеет сопловое парораспределение,
состоящее из четырех регулирующих клапанов на входе в ЦВД.
ЦВД-литой конструкции из жаропрочной стали. Проточная часть имеет
одно венечную регулирующую ступень и 16 ступеней давления.
После ЦВД пар идет в производственный отбор, а также на ЦНД и
далее в конденсатор турбины.
ЦНД состоит из трех частей:
первая до верхнего отопительного отбора имеет регулирующую
ступень и сеть ступней давления;
вторая между верхним и нижним отопительными отборами т.е.
промежуточный отсек, имеет две ступени давления;
третья часть имеет регулирующую ступень и две ступени давления.
Давление теплофикационных отборов регулируется одной поворотной
диафрагмой. Ротор высокого давления (РВД) - цельнокованый, а ротор
низкого давления (РНД) комбинированный т.е. десять дисков
цельнокованых, а три насадных. Оба ротора РВД и РНД - гибкие. Роторы
турбин соединены между собой и ротором генератора жесткими муфтами и
имеют общий упорный подшипник. Вращение ротора по часовой стрелке
если смотреть со стороны переднего подшипника. Фикс-пункт турбины
расположен на задней фундаментной раме ЦНД.
Таблица 1. Основные параметры турбин ПТ-80\100-130\13, Р-50-130/13,
Т-110/120-1
Принципиальные тепловые схемы турбоустановок ПТ-80\100-130\13,
Р-50-130/13, Т-110/120-130, Продольный разрез паровой турбины Т-110/120-
130 указаны в приложении А.
В дипломном проекте будет рассматриваться турбоустановка Т-
110/120-130.
1.3 Техническое описание и характеристика котлов БКЗ-420-140
Котлоагрегат ветикально-водотрубный, барабанный, с естественной
циркуляцией, П - образной компоновки, в газоплотном исполнении с
твердым шлакоудалением.
Топочная камера призматическая открытого типа, выполнена из
цельносварных мембранных газоплотных панелей, из цельносварных
мембранных газоплотных панелей, изготовленных из труб диаметром 60 мм
с толщиной стенки 6 мм (ст. 20), с варной полосой 20 х 6 мм. Шаг труб в
панелях - 80 мм.
Шлакоудаление твердое, со шнековыми транспортерами и дробилкой.
Топка оборудована шестью вихревыми горелками, расположенными в
два яруса на фронтовой стене.
Барабан котла сварной конструкции с внутренним диаметром 1600 мм
с толщиной стенки 112 мм (ст. 16 ГНМА).
Пароперегреватель радиационно - конвективный. Состоит из ширм d х
S = 42 х 5 мм (ст. 12X1МФ) и конвективной части из труб d х S = 38 х 4 мм;
38 х 4,5 мм; 38 х 5 мм; 38 х 6 мм (ст. 20; 12Х1МФ).
Температура перегрева пара регулируется впрыскивающим
пароохладителем, установленном в рассечку между ступенями
пароперегревателя.
В конвективной шахте размещены водяной экономайзер и трубчатый
воздухоподогреватель, скомпонованные в «рассечку». Водяной экономайзер
состоит из гладких труб из стали 20 с d х S = 32 х 4 мм.
Кубы воздухоподогреватель выполнены из труб d х S = 40 х 1.5 мм,
сталь 3.
Таблица 1.2 Техническая характеристика котла БКЗ-420 140
1.4 Технологическое описание турбины
1.4.1 Классификация паровых турбин
Паровая турбина (далее ПТ), первичный паровой двигатель с
вращательным движением рабочего органа — ротора и непрерывным
рабочим процессом; служит для преобразования тепловой энергии пара
водяного в механическую работу. Поток водяного пара поступает через
направляющие аппараты на криволинейные лопатки, закрепленные по
окружности ротора, и, воздействуя на них, приводит ротор во вращение
В зависимости от характера теплового процесса ПТ. обычно
подразделяют на 3 основные группы: чисто конденсационные,
теплофикационные и специального назначения.
Чисто конденсационные ПТ служат для превращения максимально
возможной части теплоты пара в механическую работу. Эти ПТ работают с
выпуском отработавшего пара в конденсатор, где поддерживается вакуум.
Чисто конденсационные ПТ могут быть стационарными или транспортными.
Стационарные ПТ в соединении с генераторами переменного электрическог
тока (турбогенераторы — основное оборудование конденсационных
электростанций. Чем больше мощность турбогенератора, тем он экономичнее
и тем ниже стоимость 1 кВт установленной мощности. В зависимости от
назначения ПТ для электростанций могут быть базовыми, несущими
постоянную основную нагрузку; пиковыми, кратковременно работающими
для покрытия пиков нагрузки; турбинами собственных нужд,
обеспечивающими потребность электростанции в электроэнергии. От
базовых ПТ требуется высокая экономичность на нагрузках, близких к
полной (около 80%), от пиковых ПТ — возможность быстрого пуска и
включения в работу, от ПТ собственных нужд — особая надёжность в
работе. Все ПТ для электростанций рассчитываются на 100 тыс. ч работы (до
капитального ремонта).
Теплофикационные ПТ служат для одновременного получения
электрической и тепловой энергии. К ним относятся ПТ с противодавлением,
с регулируемым отбором пара, а также с отбором и противодавлением. У ПТ
противодавлением весь отработавший пар используется для технологических
целей (варка, сушка, отопление). Электрическая мощность, развиваемая
турбоагрегатом с ПТ,зависит от потребности производства или
отопительной системы в греющем паре и меняется вместе с ней. Поэтому
турбоагрегат с противодавлением обычно работает параллельно с
конденсационной ПТ или электросетью, которые покрывают возникающий
дефицит в электроэнергии. В ПТ с регулируемым отбором часть пара
отводится из 1 или 2 промежуточных ступеней, а остальной пар идёт в
конденсатор. Давление отбираемого пара поддерживается в заданных
пределах системой регулирования. Место отбора (ступень ПТ) выбирают в
зависимости от нужных параметров пара. У ПТ с отбором и
противодавлением часть пара отводится из 1 или 2 промежуточных ступеней,
а весь отработавший пар направляется из выпускного патрубка в
отопительную систему. Давление пара ПТ для отопительных целей обычно
составляет 0,12 Мн/м2,а для технологических нужд (сахарные,
деревообрабатывающие, пищевые предприятия) 0,5—1,5 Мн/м2.
Все стационарные ПТ имеют нерегулируемые отборы пара из 2—5
ступеней давления для регенеративного подогрева питательной воды.
Установлено 4 ступени начальных параметров пара: давление 3,5 Мн/м2,
температура 435 °С для ПТ мощностью до 12 Мвт; 9 Мн/м2, 535 °С для ПТ до
50 Мвт; 13 Мн/м2, 565 °С для ПТ до 100 Мвт и 24 Мн/м2, 565 °С для Паровых
турбин мощностью 200 и 300 мВт. Давление отработавшего пара 3,5—
5 кн/м2. Удельный расход тепла от 7,6 кДж/ ( вт×ч) у самых мощных ПТ до
13 кдж/(вт×ч) у небольших конденсационных турбин.
1.4.2. Тепловой процесс паровых турбин
Кинетическая энергия, приобретённая паром при его расширении,
эквивалентна уменьшению его энтальпии в процессе расширения. Работа
пара (в кгс×м, 1 кгс×м = 10 Дж) равна:
W= 427(i0 - i1),
а скорость истечения (в м /сек):(1.1)(1.2)где i0 — начальная, a i1 — конечная энтальпия пара. Мощность (в кВт),
которую можно получить от турбины при расходе пара D кг/ч, равна:(1.3)а расход пара (в кг/ч) соответственн(1.4)
Если под i0 — i1 подразумевается адиабатическое изменение энтальпии,
то вышесказанное справедливо только для идеальной ПТ, работающей без
потерь. Действительная мощность на валу реальной Паровой турбины (в кВт )
равна:(1.5)
где hое — относительно эффективный КПД, представляющий собой
отношение действительной мощности, полученной на валу Паровой
турбины, к мощности идеальной турбины.(1.6)
где de — расход пара в кг/(кВт×ч). Для существующих Паровых турбин
удельный расход пара определяется экспериментально, а i0 — i1 находят
по i —s диаграмме. В активной ПТ свежий пар с давлением p0 и скоростью c0
поступает в сопло и расширяется в нём до давления p1, при этом скорость
пара возрастает до c1, с которой поток пара и входит на рабочие лопатки.
Поток пара, оказывая давление на лопатки вследствие изменения
направления в криволинейных междулопаточных каналах, заставляет диск и
вал вращаться. На выходе с лопаток поток пара имеет скорость c2 меньшую,
чем c1, так как значительная часть кинетической энергии преобразовалась в
механическую энергию вращения вала. Давление p1 на входе в канал равно
давлению p2 на выходе из него, так как междулопаточные каналы имеют
одинаковое сечение по длине и расширения пара в них не происходит (у
реально существующих активных турбин сечения междулопаточных каналов
выполняют несколько возрастающими по ходу пара для сохранения
равенства давлений на входе и выходе, так как энтальпия пара при его
протекании между лопатками увеличивается из - за трения и ударов о кромки
лопаток). Однако в различных местах криволинейного канала давления
неодинаковы: именно разность давлений на вогнутую и выпуклую сторону
каждой лопатки создаёт момент, заставляющий ротор вращаться. Таким
образом, в активной турбине падение давления пара происходит в сопле (или
нескольких соплах), а давление пара при входе на лопатки и выходе с них
одинаково.
Кинетическая энергия будет полностью использована, если абсолютная
скорость пара c2 при выходе с лопаток равна нулю. Это условие соблюдено,
если c1 = 2u, где u — окружная скорость. Окружная скорость (в м/сек ) равна:(1.7)
где d — средний диаметр лопаточного венца в м, a n — частота
вращения в мин. Следовательно, оптимальная окружная скорость лопаток должна быть(1.8)
Очевидно, что в реальной турбине c2не может быть равна 0, т.к. пар
должен уходить с лопаток в конденсатор. Однако выходную скорость
стремятся получить минимальной, т.к. кинетическая энергия уходящего
потока пара представляет собой потерю полезной работы. Отступление от
оптимального отношения вызывает сильное снижение КПД турбины. Это
делает невозможным создание одноступенчатых турбин с высокими
начальными параметрами пара, так как ещё не существует материалов,
способных выдержать напряжения от центробежных сил при окружных
скоростях, значительно превышающих 400 м/сек . Поэтому одноступенчатые
активные турбины применяют только для привода быстроходных
вспомогательных механизмов, экономичность которых не имеет решающего значения.
Хорошая экономичность ПТ, работающей с умеренными окружными скоростями при большом тепло падении,достигается
применением ступеней давления.
Если разделить располагаемый перепад давления на несколько
ступеней с равными перепадами тепла, то в этих ступенях скорость
истечения (в м/сек) равна:(1.9)
где z — число ступеней. Следовательно, в каждой ступени скорость
будет в раз меньше, чем в одноступенчатой ПТ. Соответственно ниже
будет, и оптимальная окружная скорость u, то есть частота вращения ротора.
Корпус ПТ с несколькими ступенями давления разделяют диафрагмами
на отдельные камеры, в каждой из которых помещен один из дисков с
рабочими лопатками. Пар может проникать из одной камеры в другую
только через сопла, расположенные по окружности диафрагм. Давление пара
снижается после каждой ступени, а скорости истечения пара c1остаются
примерно одинаковыми, что достигается выбором соответствующих
размеров сопел. Число ступеней давления у мощных турбин с высокими
начальными параметрами пара достигает 30—40. Поскольку объём пара по
мере его расширения увеличивается, сечения сопел и высоты лопаток
возрастают от первой ступени к последней. Последние ступени мощных ПТ
обычно выполняют сдвоенными, а у самых больших ПТ — строенными и
даже счетверёнными ввиду неприемлемо больших размеров лопаток
последних ступеней, которые были бы необходимы для пропуска всего
объёма пара через 1 ступень.
В ступени давления возможно использовать кинетическую энергию не
в одном, а в нескольких венцах лопаток, применив ступе ни скорости. Для
этого на ободе диска размещают 2 (редко 3) венца рабочих лопаток, между
которыми установлен венец неподвижных направляющих лопаток. Пар с
давлением p0 подводится к соплам и со скоростью c1 поступает на первый
ряд рабочих лопаток, где его скоростной напор частично превращается в
работу, а направление потока изменяется. Выйдя со скоростью c2 с первого
ряда рабочих лопаток, пар проходит через направляющие лопатки и, снова
изменив направление, входит во второй ряд лопаток со скоростью c’1,
несколько меньшей, чем c2, вследствие потерь в направляющих лопатках.
Второй ряд лопаток пар покидает с незначительной скоростью c’2.
Теоретически при 2 ступенях скорости оптимальная окружная
скорость u будет в 2 раза меньше, чем для одно венечной ступени,
использующей тот же перепад энтальпии. Для z ступеней скорости
оптимальная(1.10)
Однако много ступеней скорости практически не применяют из-за
больших потерь в лопатках. Наиболее распространённым типом турбины
можно считать активную ПТ с одним двухвенечным диском в первой
ступени давления и одновенечными дисками в остальных ступенях. Значение
двухвенечного диска в том, что, используя значительную часть
располагаемого перепада энтальпии в первой ступени давления, он позволяет
понизить температуру и давление в корпусе ПТ и одновременно уменьшить
нужное число ступеней давления, то есть укоротить и удешевить ПТ.
Конструкция паровых турбин. По направлению движения потока пара
различают аксиальные ПТ, у которых поток пара движется вдоль оси
турбины, и радиальные ПТ, направление потока пара в которых
перпендикулярно, а рабочие лопатки расположены параллельно оси
вращения. В СНГ строят только аксиальные ПТ. По числу корпусов
(цилиндров) ПТ подразделяют на однокорпусные и 2 -3- , редко 4 - корпусные.
Многокорпусная конструкция позволяет использовать большие
располагаемые перепады энтальпии, разместив большое число ступеней
давления, применить высококачественные металлы в части высокого
давления и раздвоение потока пара в части низкого давления; однако такая
ПТ получается более дорогой, тяжёлой и сложной. По числу валов различают
одновальные ПТ, у которых валы всех корпусов находятся на одной оси, и 2 -,
редко 3- вальные, состоящие из 2 или 3 параллельно размещенных
одновальных ПТ, связанных общностью теплового процесса, а у судовых ПТ
— также общей зубчатой передачей (редуктором).
Неподвижную часть ПТ - корпус - выполняют разъёмной в
горизонтальной плоскости для возможности монтажа ротора. В корпусе
имеются выточки для установки диафрагм, разъём которых совпадает с
плоскостью разъёма корпуса. По периферии диафрагм размещены сопловые
каналы, образованные криволинейными лопатками, залитыми в тело
диафрагм или приваренными к нему. В местах прохода вала сквозь стенки
корпуса установлены концевые уплотнения лабиринтового ти па для
предупреждения утечек пара наружу (со стороны высокого давления) и
засасывания воздуха в корпус (со стороны низкого). Лабиринтовые
уплотнения устанавливают в местах прохода ротора сквозь диафрагмы во
избежание перетечек пара из ступени в ступень в обход сопел. На переднем
конце вала устанавливают предельный регулятор (регулятор безопасности),
автоматически останавливающий ПТ при увеличении частоты вращения на
10—12%сверх номинальной. Задний конец ротора снабжают
валоповоротным устройством с электрическим приводом для медленного
(4 —6 об/мин ) проворачивания ротора после останова ПТ, что необходимо
для равномерного его остывания. Продольный разрез паровой турбины Т -
110/120-130 указана в «приложении А».....
Введение
1.1. Описание основного оборудования АТЭЦ-2.
1.2. Технические описания и характеристики турбин.
1.3. Техническое описание и характеристика котлов БКЗ-420-140
1.4. Технологическое описание турбины.
1.4.1 Классификация паровых турбин.
1.4.2. Тепловой процесс паровых турбин.
1.5 . Система защиты турбины
1.6 Механические величины турбины и обоснование замены 20
оборудования
1.6.1 Контролируемые объекты на турбине.
1.6.2 Обоснование замены оборудования
2. Анализ и выбор оборудования.
2.1. Первичное оборудование
2.2. Вторичное оборудование ЛМЗ-97.09С
2.2.1 Общие сведения об аппаратуре "ЛМЗ-97.09С"
2.2.2 Описание и работа
2.2.3 Шкаф аппаратный
2.3 Схемы подключения оборудования ЛМЗ
3. Анализ и разработка программного обеспечения мониторинга
механических величин турбины
4. Безопасность жизнедеятельности
4.1. Анализ условий труда
4.2. Расчет выбросов в атмосферу
4.2.1 Выброс золы в атмосферу
4.2.2 Выброс сернистого ангидрида в атмосферу.
4.2.3 Количество выбросов оксидов азота на ТЭЦ
4.2.4 Количество выбросов оксидов ванадия
4.2.5 Определение минимальной высоты трубы
4.3. Расчёт максимальной концентрации вредных веществ
5. Технико-экономическое обоснование
5.1. Цели и задачи проекта
5.2. Производимые продукты
5.3 Расчет затрат на производство тепла и электричества
5.3.1. Техническое описание производства
5.3.2. Определение затрат на топливо
5.3.3 Расчет КПД использования топлива.
5.3.4 Расчет затрат на воду.
5.3.5 Расчет затрат на заработную плату.
5.3.6 Расчет амортизационных отчислений.
5.3.7 Расчет затрат на проведение текущего ремонта.
5.3.8 Расчет платы за выбросы.
5.3.9 Общестанционные и цеховые расходы.
5.4. Расчет себестоимости отпуска энергии.
5.5. Расчет затрат на систему мониторинга.
5.5.1 Расчет затрат на оборудование ЛМЗ97 -09С
5.6. Ожидаемый экономический эффект модернизации турбины
Заключение.
Список литературы
Приложение А
Приложение Б
Приложение В
Приложение Г
Приложение Д
Приложение Е
Приложение Ж
Приложение З
Приложение И
Приложение К
1. Общая часть. Описание объекта автоматизации
1.1 Описание основного оборудования АТЭЦ-2
а) шесть паровых турбин три турбины типа ПТ-80/100-130/13; одна
турбина типа Р-50-130; две турбины типа Т-100/120-130.
б) семь паровых котлов типа БКЗ-420-140.
1.2 Технические описания и характеристики турбин
Паровая турбина ПТ-80/100-130/13, конденсационная с регулируемыми
отборами пара производственным и отопительными, номинальной
мощностью 80 МВт. Представляет собой одновальный двухцилиндровый
агрегат и предназначен для непосредственного привода генератора типа
ТВФ-120-2 мощностью 120 МВт.
Турбина ПТ-80/100-130/130 имеет сопловое парораспределение,
состоящее из четырех регулирующих клапанов на входе в ЦВД.
ЦВД-литой конструкции из жаропрочной стали. Проточная часть имеет
одно венечную регулирующую ступень и 16 ступеней давления.
После ЦВД пар идет в производственный отбор, а также на ЦНД и
далее в конденсатор турбины.
ЦНД состоит из трех частей:
первая до верхнего отопительного отбора имеет регулирующую
ступень и сеть ступней давления;
вторая между верхним и нижним отопительными отборами т.е.
промежуточный отсек, имеет две ступени давления;
третья часть имеет регулирующую ступень и две ступени давления.
Давление теплофикационных отборов регулируется одной поворотной
диафрагмой. Ротор высокого давления (РВД) - цельнокованый, а ротор
низкого давления (РНД) комбинированный т.е. десять дисков
цельнокованых, а три насадных. Оба ротора РВД и РНД - гибкие. Роторы
турбин соединены между собой и ротором генератора жесткими муфтами и
имеют общий упорный подшипник. Вращение ротора по часовой стрелке
если смотреть со стороны переднего подшипника. Фикс-пункт турбины
расположен на задней фундаментной раме ЦНД.
Таблица 1. Основные параметры турбин ПТ-80\100-130\13, Р-50-130/13,
Т-110/120-1
Принципиальные тепловые схемы турбоустановок ПТ-80\100-130\13,
Р-50-130/13, Т-110/120-130, Продольный разрез паровой турбины Т-110/120-
130 указаны в приложении А.
В дипломном проекте будет рассматриваться турбоустановка Т-
110/120-130.
1.3 Техническое описание и характеристика котлов БКЗ-420-140
Котлоагрегат ветикально-водотрубный, барабанный, с естественной
циркуляцией, П - образной компоновки, в газоплотном исполнении с
твердым шлакоудалением.
Топочная камера призматическая открытого типа, выполнена из
цельносварных мембранных газоплотных панелей, из цельносварных
мембранных газоплотных панелей, изготовленных из труб диаметром 60 мм
с толщиной стенки 6 мм (ст. 20), с варной полосой 20 х 6 мм. Шаг труб в
панелях - 80 мм.
Шлакоудаление твердое, со шнековыми транспортерами и дробилкой.
Топка оборудована шестью вихревыми горелками, расположенными в
два яруса на фронтовой стене.
Барабан котла сварной конструкции с внутренним диаметром 1600 мм
с толщиной стенки 112 мм (ст. 16 ГНМА).
Пароперегреватель радиационно - конвективный. Состоит из ширм d х
S = 42 х 5 мм (ст. 12X1МФ) и конвективной части из труб d х S = 38 х 4 мм;
38 х 4,5 мм; 38 х 5 мм; 38 х 6 мм (ст. 20; 12Х1МФ).
Температура перегрева пара регулируется впрыскивающим
пароохладителем, установленном в рассечку между ступенями
пароперегревателя.
В конвективной шахте размещены водяной экономайзер и трубчатый
воздухоподогреватель, скомпонованные в «рассечку». Водяной экономайзер
состоит из гладких труб из стали 20 с d х S = 32 х 4 мм.
Кубы воздухоподогреватель выполнены из труб d х S = 40 х 1.5 мм,
сталь 3.
Таблица 1.2 Техническая характеристика котла БКЗ-420 140
1.4 Технологическое описание турбины
1.4.1 Классификация паровых турбин
Паровая турбина (далее ПТ), первичный паровой двигатель с
вращательным движением рабочего органа — ротора и непрерывным
рабочим процессом; служит для преобразования тепловой энергии пара
водяного в механическую работу. Поток водяного пара поступает через
направляющие аппараты на криволинейные лопатки, закрепленные по
окружности ротора, и, воздействуя на них, приводит ротор во вращение
В зависимости от характера теплового процесса ПТ. обычно
подразделяют на 3 основные группы: чисто конденсационные,
теплофикационные и специального назначения.
Чисто конденсационные ПТ служат для превращения максимально
возможной части теплоты пара в механическую работу. Эти ПТ работают с
выпуском отработавшего пара в конденсатор, где поддерживается вакуум.
Чисто конденсационные ПТ могут быть стационарными или транспортными.
Стационарные ПТ в соединении с генераторами переменного электрическог
тока (турбогенераторы — основное оборудование конденсационных
электростанций. Чем больше мощность турбогенератора, тем он экономичнее
и тем ниже стоимость 1 кВт установленной мощности. В зависимости от
назначения ПТ для электростанций могут быть базовыми, несущими
постоянную основную нагрузку; пиковыми, кратковременно работающими
для покрытия пиков нагрузки; турбинами собственных нужд,
обеспечивающими потребность электростанции в электроэнергии. От
базовых ПТ требуется высокая экономичность на нагрузках, близких к
полной (около 80%), от пиковых ПТ — возможность быстрого пуска и
включения в работу, от ПТ собственных нужд — особая надёжность в
работе. Все ПТ для электростанций рассчитываются на 100 тыс. ч работы (до
капитального ремонта).
Теплофикационные ПТ служат для одновременного получения
электрической и тепловой энергии. К ним относятся ПТ с противодавлением,
с регулируемым отбором пара, а также с отбором и противодавлением. У ПТ
противодавлением весь отработавший пар используется для технологических
целей (варка, сушка, отопление). Электрическая мощность, развиваемая
турбоагрегатом с ПТ,зависит от потребности производства или
отопительной системы в греющем паре и меняется вместе с ней. Поэтому
турбоагрегат с противодавлением обычно работает параллельно с
конденсационной ПТ или электросетью, которые покрывают возникающий
дефицит в электроэнергии. В ПТ с регулируемым отбором часть пара
отводится из 1 или 2 промежуточных ступеней, а остальной пар идёт в
конденсатор. Давление отбираемого пара поддерживается в заданных
пределах системой регулирования. Место отбора (ступень ПТ) выбирают в
зависимости от нужных параметров пара. У ПТ с отбором и
противодавлением часть пара отводится из 1 или 2 промежуточных ступеней,
а весь отработавший пар направляется из выпускного патрубка в
отопительную систему. Давление пара ПТ для отопительных целей обычно
составляет 0,12 Мн/м2,а для технологических нужд (сахарные,
деревообрабатывающие, пищевые предприятия) 0,5—1,5 Мн/м2.
Все стационарные ПТ имеют нерегулируемые отборы пара из 2—5
ступеней давления для регенеративного подогрева питательной воды.
Установлено 4 ступени начальных параметров пара: давление 3,5 Мн/м2,
температура 435 °С для ПТ мощностью до 12 Мвт; 9 Мн/м2, 535 °С для ПТ до
50 Мвт; 13 Мн/м2, 565 °С для ПТ до 100 Мвт и 24 Мн/м2, 565 °С для Паровых
турбин мощностью 200 и 300 мВт. Давление отработавшего пара 3,5—
5 кн/м2. Удельный расход тепла от 7,6 кДж/ ( вт×ч) у самых мощных ПТ до
13 кдж/(вт×ч) у небольших конденсационных турбин.
1.4.2. Тепловой процесс паровых турбин
Кинетическая энергия, приобретённая паром при его расширении,
эквивалентна уменьшению его энтальпии в процессе расширения. Работа
пара (в кгс×м, 1 кгс×м = 10 Дж) равна:
W= 427(i0 - i1),
а скорость истечения (в м /сек):(1.1)(1.2)где i0 — начальная, a i1 — конечная энтальпия пара. Мощность (в кВт),
которую можно получить от турбины при расходе пара D кг/ч, равна:(1.3)а расход пара (в кг/ч) соответственн(1.4)
Если под i0 — i1 подразумевается адиабатическое изменение энтальпии,
то вышесказанное справедливо только для идеальной ПТ, работающей без
потерь. Действительная мощность на валу реальной Паровой турбины (в кВт )
равна:(1.5)
где hое — относительно эффективный КПД, представляющий собой
отношение действительной мощности, полученной на валу Паровой
турбины, к мощности идеальной турбины.(1.6)
где de — расход пара в кг/(кВт×ч). Для существующих Паровых турбин
удельный расход пара определяется экспериментально, а i0 — i1 находят
по i —s диаграмме. В активной ПТ свежий пар с давлением p0 и скоростью c0
поступает в сопло и расширяется в нём до давления p1, при этом скорость
пара возрастает до c1, с которой поток пара и входит на рабочие лопатки.
Поток пара, оказывая давление на лопатки вследствие изменения
направления в криволинейных междулопаточных каналах, заставляет диск и
вал вращаться. На выходе с лопаток поток пара имеет скорость c2 меньшую,
чем c1, так как значительная часть кинетической энергии преобразовалась в
механическую энергию вращения вала. Давление p1 на входе в канал равно
давлению p2 на выходе из него, так как междулопаточные каналы имеют
одинаковое сечение по длине и расширения пара в них не происходит (у
реально существующих активных турбин сечения междулопаточных каналов
выполняют несколько возрастающими по ходу пара для сохранения
равенства давлений на входе и выходе, так как энтальпия пара при его
протекании между лопатками увеличивается из - за трения и ударов о кромки
лопаток). Однако в различных местах криволинейного канала давления
неодинаковы: именно разность давлений на вогнутую и выпуклую сторону
каждой лопатки создаёт момент, заставляющий ротор вращаться. Таким
образом, в активной турбине падение давления пара происходит в сопле (или
нескольких соплах), а давление пара при входе на лопатки и выходе с них
одинаково.
Кинетическая энергия будет полностью использована, если абсолютная
скорость пара c2 при выходе с лопаток равна нулю. Это условие соблюдено,
если c1 = 2u, где u — окружная скорость. Окружная скорость (в м/сек ) равна:(1.7)
где d — средний диаметр лопаточного венца в м, a n — частота
вращения в мин. Следовательно, оптимальная окружная скорость лопаток должна быть(1.8)
Очевидно, что в реальной турбине c2не может быть равна 0, т.к. пар
должен уходить с лопаток в конденсатор. Однако выходную скорость
стремятся получить минимальной, т.к. кинетическая энергия уходящего
потока пара представляет собой потерю полезной работы. Отступление от
оптимального отношения вызывает сильное снижение КПД турбины. Это
делает невозможным создание одноступенчатых турбин с высокими
начальными параметрами пара, так как ещё не существует материалов,
способных выдержать напряжения от центробежных сил при окружных
скоростях, значительно превышающих 400 м/сек . Поэтому одноступенчатые
активные турбины применяют только для привода быстроходных
вспомогательных механизмов, экономичность которых не имеет решающего значения.
Хорошая экономичность ПТ, работающей с умеренными окружными скоростями при большом тепло падении,достигается
применением ступеней давления.
Если разделить располагаемый перепад давления на несколько
ступеней с равными перепадами тепла, то в этих ступенях скорость
истечения (в м/сек) равна:(1.9)
где z — число ступеней. Следовательно, в каждой ступени скорость
будет в раз меньше, чем в одноступенчатой ПТ. Соответственно ниже
будет, и оптимальная окружная скорость u, то есть частота вращения ротора.
Корпус ПТ с несколькими ступенями давления разделяют диафрагмами
на отдельные камеры, в каждой из которых помещен один из дисков с
рабочими лопатками. Пар может проникать из одной камеры в другую
только через сопла, расположенные по окружности диафрагм. Давление пара
снижается после каждой ступени, а скорости истечения пара c1остаются
примерно одинаковыми, что достигается выбором соответствующих
размеров сопел. Число ступеней давления у мощных турбин с высокими
начальными параметрами пара достигает 30—40. Поскольку объём пара по
мере его расширения увеличивается, сечения сопел и высоты лопаток
возрастают от первой ступени к последней. Последние ступени мощных ПТ
обычно выполняют сдвоенными, а у самых больших ПТ — строенными и
даже счетверёнными ввиду неприемлемо больших размеров лопаток
последних ступеней, которые были бы необходимы для пропуска всего
объёма пара через 1 ступень.
В ступени давления возможно использовать кинетическую энергию не
в одном, а в нескольких венцах лопаток, применив ступе ни скорости. Для
этого на ободе диска размещают 2 (редко 3) венца рабочих лопаток, между
которыми установлен венец неподвижных направляющих лопаток. Пар с
давлением p0 подводится к соплам и со скоростью c1 поступает на первый
ряд рабочих лопаток, где его скоростной напор частично превращается в
работу, а направление потока изменяется. Выйдя со скоростью c2 с первого
ряда рабочих лопаток, пар проходит через направляющие лопатки и, снова
изменив направление, входит во второй ряд лопаток со скоростью c’1,
несколько меньшей, чем c2, вследствие потерь в направляющих лопатках.
Второй ряд лопаток пар покидает с незначительной скоростью c’2.
Теоретически при 2 ступенях скорости оптимальная окружная
скорость u будет в 2 раза меньше, чем для одно венечной ступени,
использующей тот же перепад энтальпии. Для z ступеней скорости
оптимальная(1.10)
Однако много ступеней скорости практически не применяют из-за
больших потерь в лопатках. Наиболее распространённым типом турбины
можно считать активную ПТ с одним двухвенечным диском в первой
ступени давления и одновенечными дисками в остальных ступенях. Значение
двухвенечного диска в том, что, используя значительную часть
располагаемого перепада энтальпии в первой ступени давления, он позволяет
понизить температуру и давление в корпусе ПТ и одновременно уменьшить
нужное число ступеней давления, то есть укоротить и удешевить ПТ.
Конструкция паровых турбин. По направлению движения потока пара
различают аксиальные ПТ, у которых поток пара движется вдоль оси
турбины, и радиальные ПТ, направление потока пара в которых
перпендикулярно, а рабочие лопатки расположены параллельно оси
вращения. В СНГ строят только аксиальные ПТ. По числу корпусов
(цилиндров) ПТ подразделяют на однокорпусные и 2 -3- , редко 4 - корпусные.
Многокорпусная конструкция позволяет использовать большие
располагаемые перепады энтальпии, разместив большое число ступеней
давления, применить высококачественные металлы в части высокого
давления и раздвоение потока пара в части низкого давления; однако такая
ПТ получается более дорогой, тяжёлой и сложной. По числу валов различают
одновальные ПТ, у которых валы всех корпусов находятся на одной оси, и 2 -,
редко 3- вальные, состоящие из 2 или 3 параллельно размещенных
одновальных ПТ, связанных общностью теплового процесса, а у судовых ПТ
— также общей зубчатой передачей (редуктором).
Неподвижную часть ПТ - корпус - выполняют разъёмной в
горизонтальной плоскости для возможности монтажа ротора. В корпусе
имеются выточки для установки диафрагм, разъём которых совпадает с
плоскостью разъёма корпуса. По периферии диафрагм размещены сопловые
каналы, образованные криволинейными лопатками, залитыми в тело
диафрагм или приваренными к нему. В местах прохода вала сквозь стенки
корпуса установлены концевые уплотнения лабиринтового ти па для
предупреждения утечек пара наружу (со стороны высокого давления) и
засасывания воздуха в корпус (со стороны низкого). Лабиринтовые
уплотнения устанавливают в местах прохода ротора сквозь диафрагмы во
избежание перетечек пара из ступени в ступень в обход сопел. На переднем
конце вала устанавливают предельный регулятор (регулятор безопасности),
автоматически останавливающий ПТ при увеличении частоты вращения на
10—12%сверх номинальной. Задний конец ротора снабжают
валоповоротным устройством с электрическим приводом для медленного
(4 —6 об/мин ) проворачивания ротора после останова ПТ, что необходимо
для равномерного его остывания. Продольный разрез паровой турбины Т -
110/120-130 указана в «приложении А».....
Толық нұсқасын 30 секундтан кейін жүктей аласыз!!!
Қарап көріңіз 👇
Пайдалы сілтемелер:
» Туған күнге 99 тілектер жинағы: өз сөзімен, қысқаша, қарапайым туған күнге тілек
» Абай Құнанбаев барлық өлеңдер жинағын жүктеу, оқу
» Дастархан батасы: дастарханға бата беру, ас қайыру
Ілмектер: скачать Разработка системы мониторинга механических величин турбины бесплатно дипломную работу, база готовых дипломных работ бесплатно, готовые дипломные работы скачать бесплатно, дипломная работа скачать бесплатно казахстан, Разработка системы мониторинга механических величин турбины